Water bucket moulds play a crucial role in streamlining production processes and maximizing efficiency in various industries. These moulds are used to create water buckets of different sizes, shapes, and capacities. Here are some key benefits of using water bucket moulds to optimize production efficiency:
Consistent and Reproducible Results:
Water bucket moulds ensure consistent and reproducible results in every production cycle. The precise design and manufacturing of the moulds allow for the creation of identical water buckets with consistent dimensions, shape, and quality. This ensures uniformity in the final product, making it easier to stack, store, and transport the buckets efficiently.
Efficient Manufacturing Process:
Water bucket moulds enable fast and efficient production of water buckets. The moulds are designed to accommodate multiple cavities, allowing for the simultaneous production of multiple buckets in a single moulding cycle. This reduces production time and increases output, leading to higher productivity and cost savings.
Customization and Flexibility:
Water bucket moulds offer customization options to meet specific requirements. They can be designed to produce water buckets of various sizes, capacities, and designs according to customer demands. The flexibility of water bucket moulds allows manufacturers to cater to different market segments and adapt to changing customer preferences.
Durability and Longevity:
Water bucket moulds are typically made from high-quality materials, such as durable metals or high-grade plastics, that can withstand the demands of high-volume production. The robust construction ensures the moulds' longevity and minimizes the need for frequent replacements or repairs, reducing downtime and maintenance costs.
Enhanced Production Efficiency:
Water bucket moulds streamline the production process, resulting in improved efficiency. The moulds facilitate rapid moulding cycles, enabling manufacturers to produce a large number of water buckets within a short timeframe. This helps meet demand, reduce lead times, and optimize production schedules.
Waste Reduction:
Water bucket moulds contribute to waste reduction in the production process. The moulds are designed to minimize material waste by utilizing precise cavity dimensions that result in minimal excess material or flash. This reduces material costs and minimizes waste disposal requirements.
Cost Savings:
Using water bucket moulds can lead to significant cost savings in the long run. The increased production efficiency, reduced material waste, and improved output contribute to overall cost optimization. Moreover, the durability and longevity of the moulds reduce maintenance and replacement costs, enhancing the cost-effectiveness of the production process.
When utilizing water bucket moulds, it is crucial to work with experienced mould manufacturers who can provide customized designs, ensure quality construction, and offer technical support. Regular maintenance and proper care of the moulds are also essential to prolong their lifespan and optimize their performance.
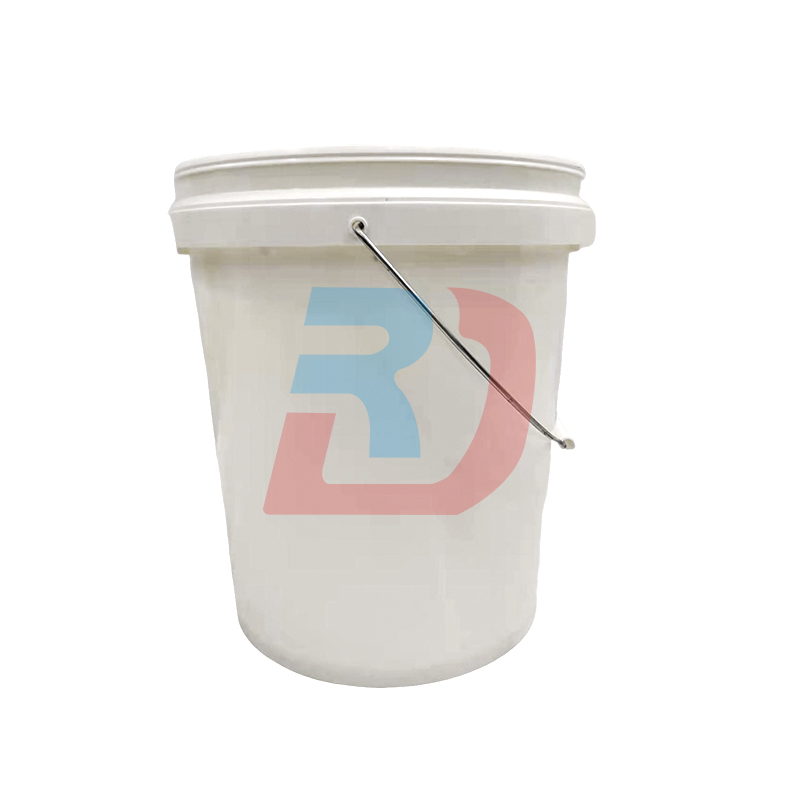
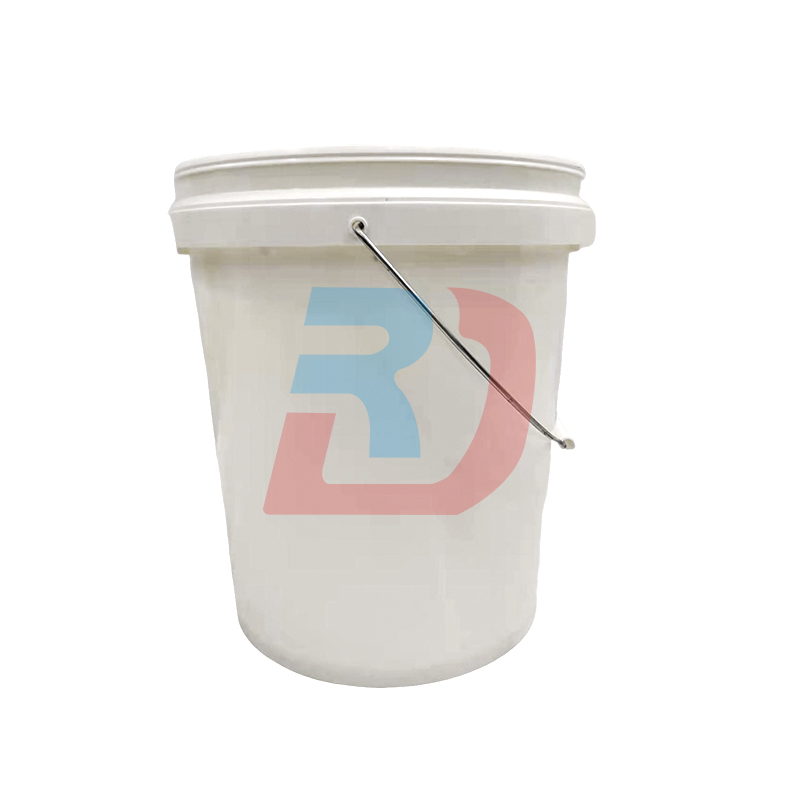
By leveraging the advantages of water bucket moulds, manufacturers can streamline production, increase efficiency, reduce costs, and meet market demands effectively.